Table 4: Top Entity Ports
Name | Port | type |
clk | in | STD_LOGIC |
sensors | in | STD_LOGIC_VECTOR (4 DOWNTO 0) |
calls | in | STD_LOGIC_VECTOR (4 DOWNTO 0) |
menu | in | STD_LOGIC_VECTOR (4 DOWNTO 0) |
motor | out | STD_LOGIC_VECTOR (1 DOWNTO 0) |
sleep | out | STD_LOGIC |
ss | out | STD_LOGIC_VECTOR (6 DOWNTO 0) |
Now we should understand all the components within the design. These components are shown in figure 5.

Fig.5:: System Components
- Counter is a 24 bit counter in the design.
- Sensors should be designed according to the following functionality
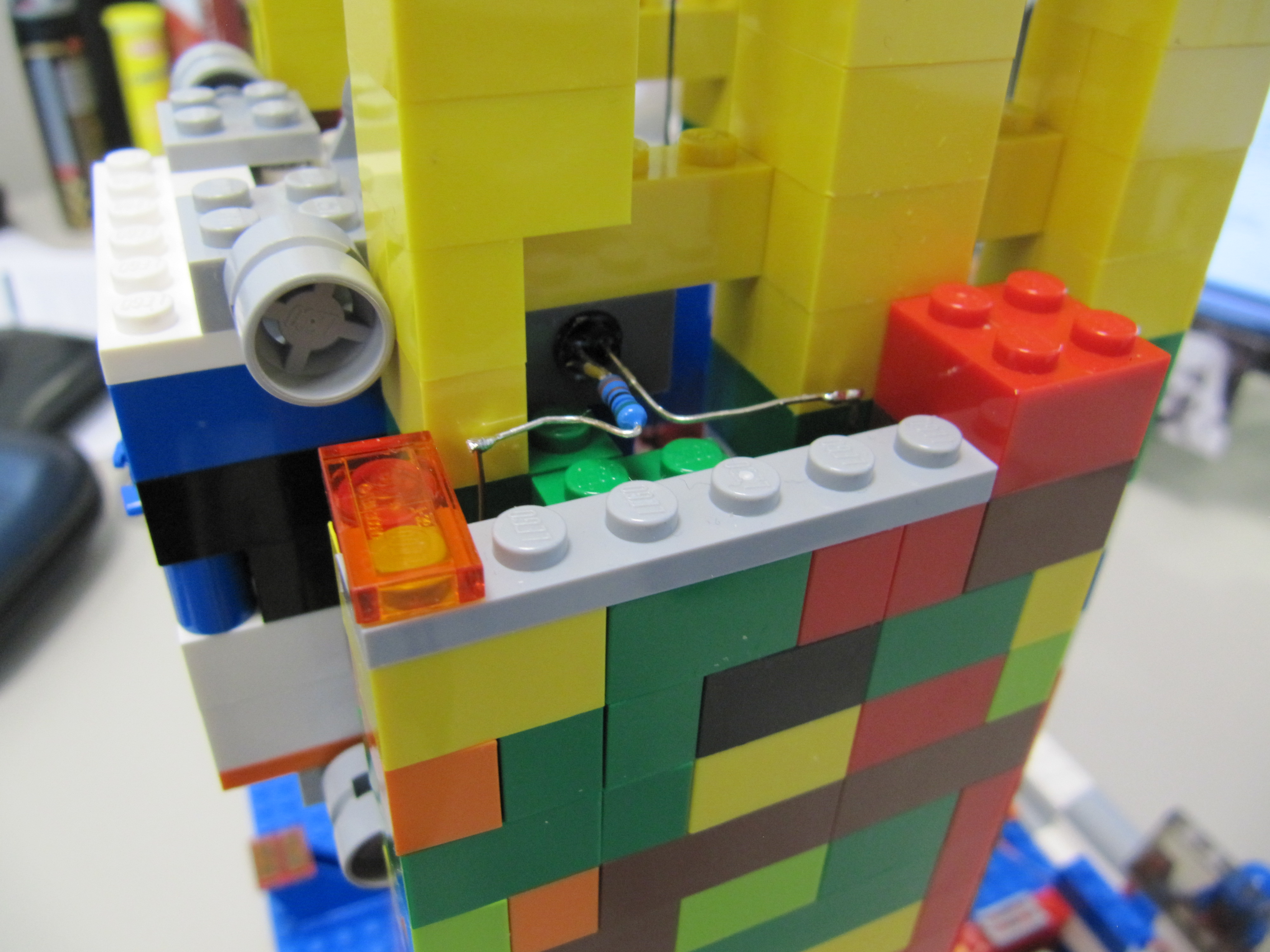
Fig.6:: Infra red sensors in the Model
- Sensors are prone to bouncing because of vibrations in the lift which might not be visible to the naked eye but is visible to the sensors.
Hence the sensors need to be de-bounced by a three bit shift register with 19th bit of counter slowing the de-bouncing circuit.
- The lift has five ray cut Infra-Red (IR) sensors.
- When ever a sensors ray is cut by the lift it sends a signal '1' to the FPGA. Otherwise the sensor sends a '0'
- Each sensor is placed between floors and there can be blind spots between each sensor. When the lift is in a blind spot all sensors send "00000" to the FPGA.
This is the time when the lift is moving between two sensors. At this point sensors can also recieve value from two sensors as well.
(e.g. on the second floor sensors can either have a value "00000" or "00110".) It is recommended that both cases should be handled by the designer.
(hint: rather then looking for sensor ="00100" look for sensor(2)= "1".)
- Seven segment should work as follows
- Seven segment decoder decodes the current floor into seven segment output.
- keep in mind that unlike seven segments on Nexys FPGAs you do not need to specify the anode.
- Each segment is turned on by logic value 1. Seven segment should also be able to blink 5 times after it reaches a floor.
- Unlike nexys 2/3 board's seven segment the pin orientation is opposite. (i-e. seven segment <= "abcdefg";)
- When the elevator reach a particular floor then it should stop and blink the floor number for 5 seconds.
- Motor should be controlled in the following manner by motor FSM
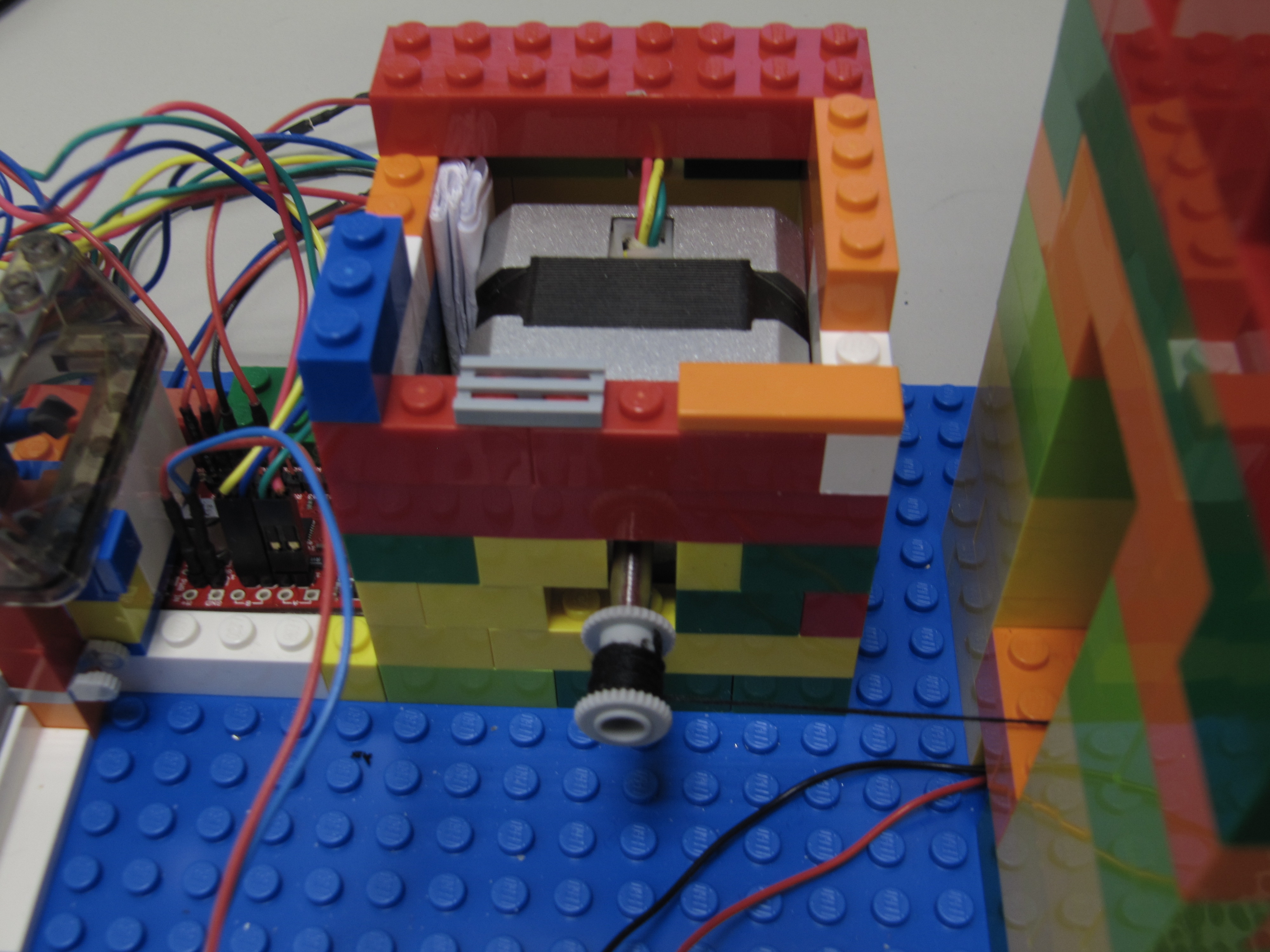
Fig.7:: Stepper motor in the model
- Motor FSM generates motor. It generates three signals.
- Motor(0) controls the direction of the motor. Where '1' is DOWN '0' is up
- Motor(1) generates a clock signal which controls the speed of the motor. The speed is specified by a clk like signal by changing its frequency.
The recommended speed of Motor can be given by sending 10th bit of the counter.
- A sleep signal turns off the motor. In idle state the motor should be kept turned off. where '1' is ON and '0' is OFF
- Motor FSM should also shares its Status with Floor FSM ( i.e. idle, going up, going down, blinking Seven segment)
- The Floor FSM should work in the following manner.
- FSM floor calculates the current floor based on the sensor and the Motor FSM status (direction sleep).
- The sensors have blind spots Hence the floor FSM should remember its own floor while passing through the blind spot
Write each component and test component them separately.
Once each block is verified according to the specifications then instantiation them together and test it.
Test the complete design against the given VHDL Test Bench
Once all the test pass, write a test bench in verilog to test the design. You may require a wrapper to integrate the VHDL design within Verilog.
Download the UCF File and implement the design on the Xula FPGA (xs3s200a-4vq100) .
You will be using XULA boards to do so. You can find Xula reference manual from "tools user guides and manuals".
To test the behavior of the lift and play with it, we have provided you a working demo that you can use to program FPGA.
NOTE: This model has 5 floors, the 5th floor is not accessible since there is a hardware break to prevent bad designs to break through the roof.
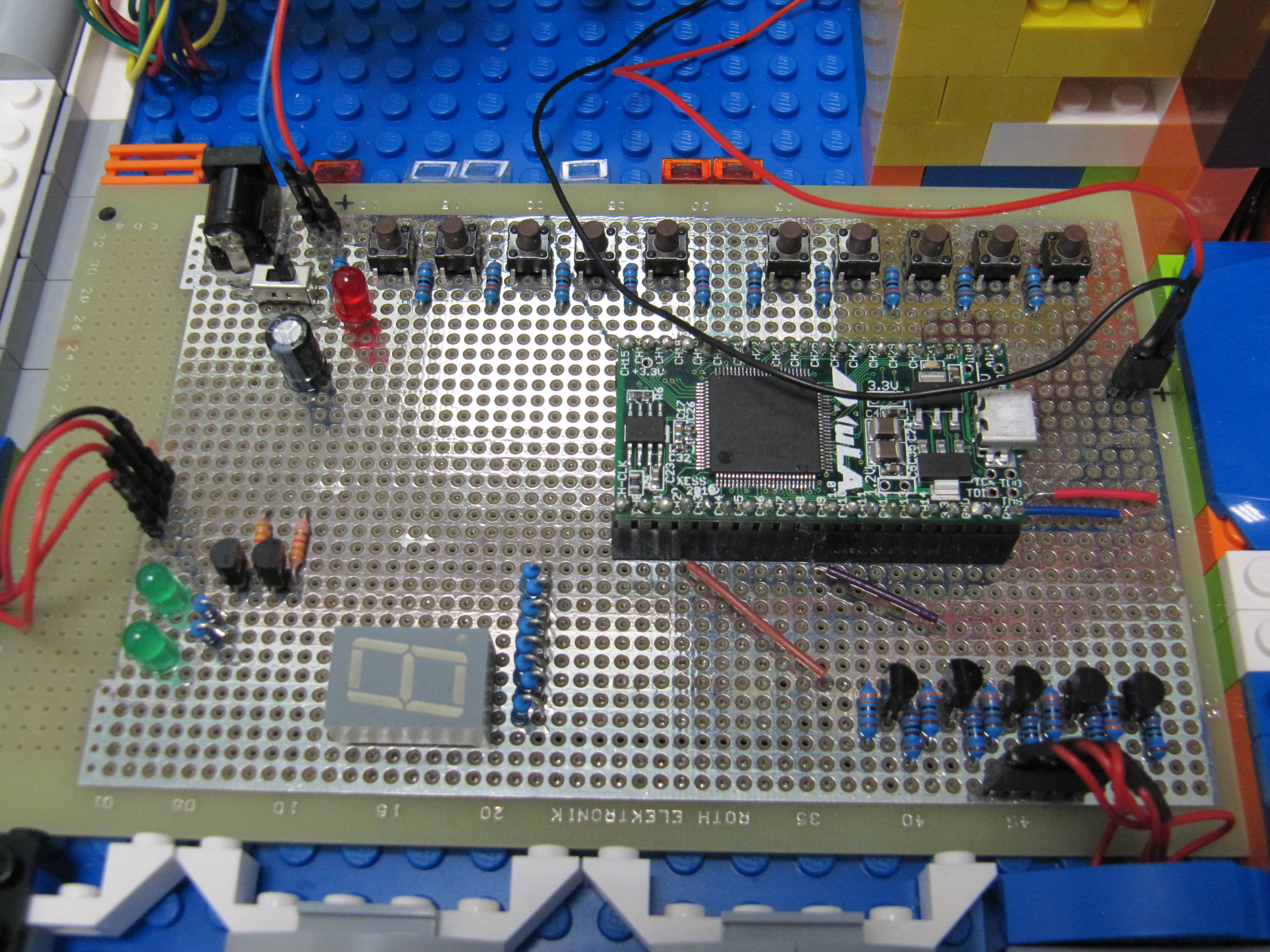
Fig.8:: Xula and prototype board

Fig.9:: schematic of prototype board
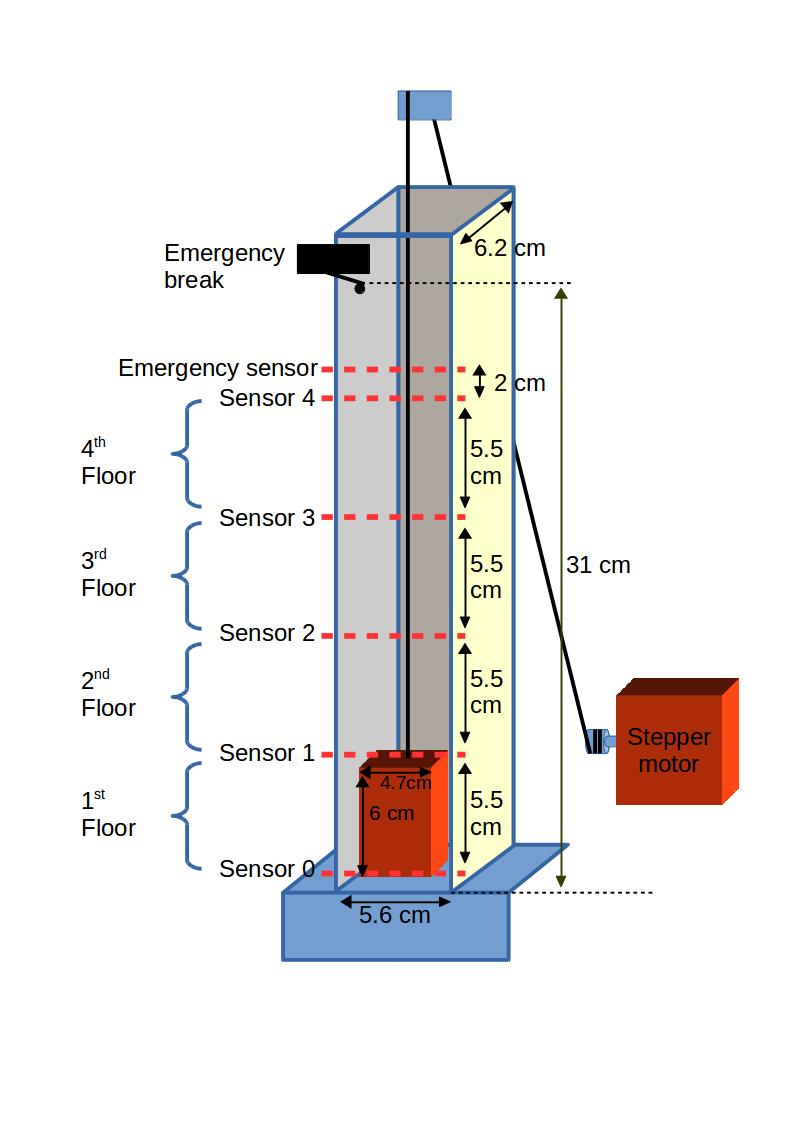
Fig.10:: schematic of the model
Write a report on this lab. write a detailed specification of each component, including State diagrams. Describe each component and motivate each decision.
Make reasonable assumptions where necessary.